Mass flow controllers (MFCs) precisely deliver fluids, mainly process gases, into bioreactors and other process systems used in biopharmaceutical production. The reliable, repeatable performance of these devices is affected by several factors — two of which can often be overlooked, by both OEMs and end users.
Metrology: what specific techniques are used to test, measure and confirm MFC accuracy
Calibration: how an MFC is calibrated on an ongoing basis
Understanding how metrology, reference standards and calibration affect long-term MFC performance – and how you can ensure proper calibration – can help sustain biopharmaceutical process system results. Metrology and calibration labs utilize a variety of instrumentation technologies and appropriate calibration reference standards. They’re the experts.
Process equipment end users can perform their own MFC calibration verification and/or recalibration, if they choose. However, selecting the correct and most trustworthy reference standard is crucial, whether for tabletop laboratory research bioreactors, pilot plants for scaling up new processes or full-scale production systems.
Selecting the most appropriate reference standard starts with defining the process uncertainty requirements. It may seem strange that we at Brooks are prepared to discuss “uncertainty” as it relates to our MFCs; after all, we emphasize their world-class accuracy, reliability and repeatability.
But understanding MFC metrology requires understanding uncertainty. In MFCs, the uncertainty in the flow measurement is a combination of the uncertainties due to systematic errors and those due to random variations (typically referred to as type B and type A errors).
To accomplish this, it makes sense to compare the measurements being made with those of the national standards.
Two types of flow standards
There are two types of standards that can be selected for MFC reference standards (typically done by the manufacturer):
Primary standards: These can be directly traced to volume (length), time, temperature and pressure readings, which are established and maintained by recognized standards bodies, such as the National Institute of Standards and Technology (NIST).
Secondary standards: Transfer or secondary standards are MFCs or other flow measurement devices that are calibrated against another standard. These secondary standards are not directly tracible to a primary standard and are one step further removed from National Laboratory traceability.
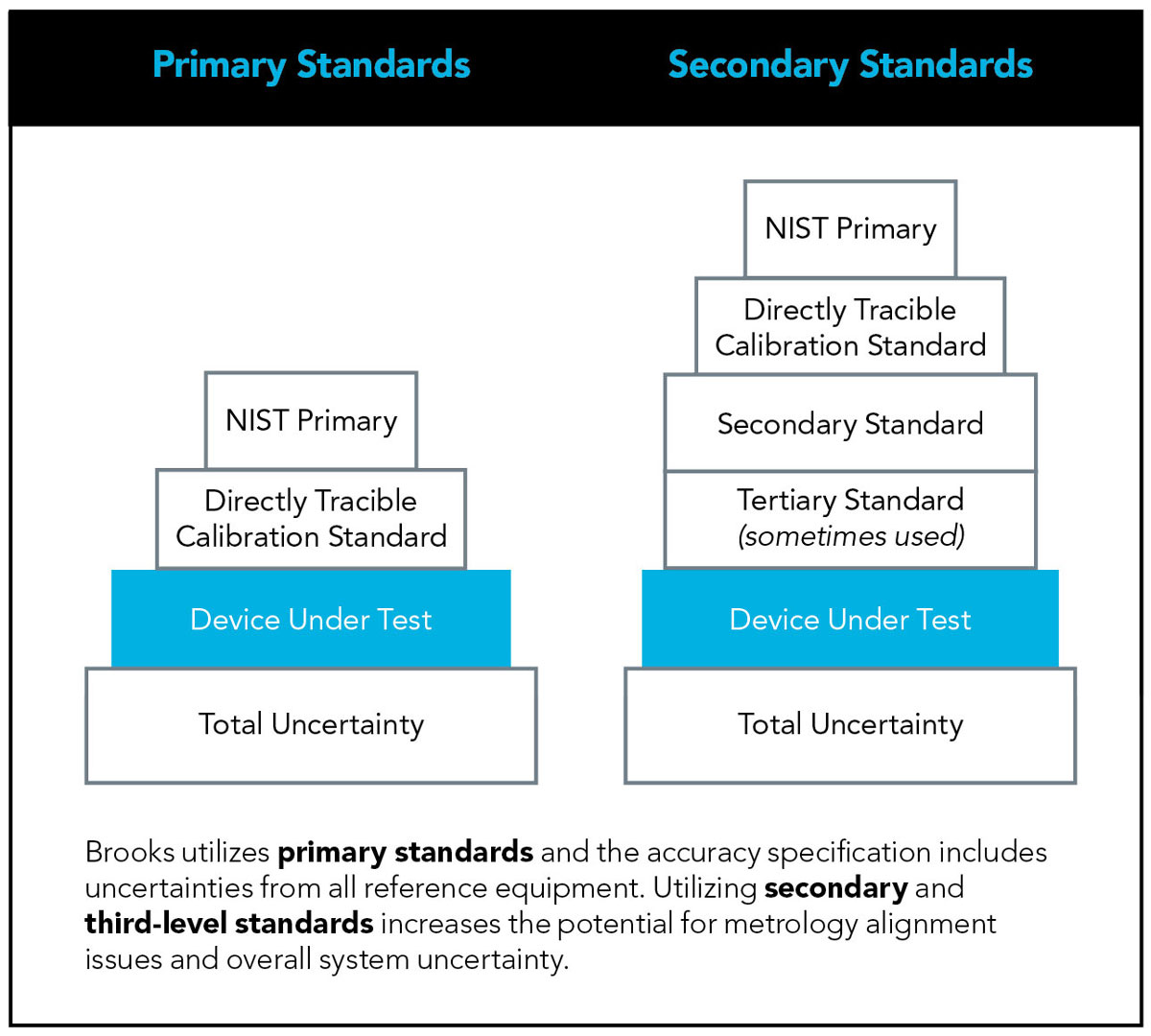
Brooks accuracy specification includes uncertainties from all reference equipment. Utilizing secondary and third-level standards increases the potential for metrology alignment issues and overall system uncertainty.
Good metrology practice is to have a Test Accuracy Ratio (TAR) of 4:1. This means the standard being used should be four times more accurate than the unit being tested. In cases where a flow standard does not meet the 4:1 recommendation for TAR, an increase to the allowable “error band” on accuracy verifications should be considered.
A fuller understanding of the principles of metrology and calibration can help you make informed decisions about how you manage the MFC technology in your bioprocessing systems.
We can provide that insight. To get the complete picture from Brooks metrology experts, download our new Biotechnology eBook: Understanding MFC Metrology & Calibration or click to find more Biotechnology Content and Insights.