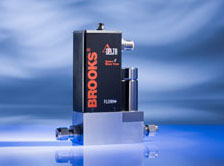
83% of all instruments used in the chemical process industries (CPI) are being talked to using analog communications. By analog communications, we mean 4-20 milliAmp mainly. But we see 3-15 psi air and 0-5 volt control systems also. Why wouldn't you use some of those 1's and 0's?
Actually, we have no idea just what percent of devices are being operated in the analog mode. 83% just seems like a good guess; although some at Brooks Instrument suggest it is much higher.
When you survey the field devices in your plant, you will find 5 major classes of instruments; flow, temperature, level, pressure, and analyzers (DO, pH, Cl2, etc…).
When the 4-20 milliAmp protocol was established and popularized in the mid 50's, we thought all instrumentation would convert and we would never have to use 3-15 psi air again. (How many I to P converters does your plant still have some 50 years later?)
4-20 mA signals travel so well, we thought no one would ever use 0-5 volt again. I think the laptop I am currently using has 5-volt commands coming and going from a number of sockets… and I know Brooks Instrument supplies 0-5 volt devices every day to a growing customer base.
But why aren't we using the digital communications?
Manufacturers of instrumentation devices are loading their instruments with bells and whistles (features!). Why can't you guys in the plant wire everything up and be happy (benefits!)?
There are two main reasons the bells and whistles with their resulting noises (features with benefits) are not being used. First, the instrument is designed to work either digitally or analog and everyone is comfortable getting the primary variable (PV) out using the analog signals. Second, a lot of plant control systems don't know what to do with the additional information available when using digital communications.
Let's analyze the first reason. Your plant has all analog controls and you receive a new device. You find an I/O slot in your control system rack and send 4-20 milliAmps to the control room. But, don't you ring it out using your HART communicator? You can change ranges, see actual values, test outputs, configure alarms, set totalizers… wait a minute, you are using digital communications! But then you turn it over to the plant operations guys and leave them with only the analog signal…
There are simple programs (adders) to your control system that will allow you to see and use the HART signals. But that technology is so "last century"…
Instrument manufactures today are outputting streams of digital information from every device. Simple devices like single point temperature and level transmitters have
RS232 communications. Advanced devices such as
thermal mass flow meters (and
thermal mass flow controllers) have
DeviceNet,
ProfiBus, and
Foundation FieldBus communications. There is so much information coming and going to these devices its no wonder a lot of you only use the analog signal.
That brings us to the second obstacle to using digital communications. Just what are you going to do with these 1's and 0's back in your control room?
If you are fortunate enough to have a massive control system from a major massive control system supplier, you have the ability to wire up the digital information and access all sorts of information; from diagnostic to informative. This could include:
- Test and check analog I\O signal level and valve drive voltage
- Data logging
- Save and restore device configuration
- Check and adjust signal response via PID tuning
- Valve adjustment for offset and span settings
There are other ways to get to the digital information. Some devices include indicating lights (count the flashes and go to the trouble shooting guide) or single contact closures (TTL) to indicate an alarm condition that, then, requires a temporary hook up to a PC to diagnose further.
There are a lot of ways to utilize the digital information the device manufacturers are providing. You just need to realize the value to your process and find a way to wire them up.
Component datasource missing. Select a datasource for this component.