
The many challenges associated with mining natural diamonds has led to the development of manufacturing synthetic diamonds. Grown in a lab, synthetic diamonds have become an attractive alternative to natural diamonds for a variety of reasons including:
- Protecting the environment
- Protecting human rights associated with natural diamond mining
- Lowering production costs and
- Virtually unlimited supply
The production of lab-grown diamonds, depending on the desired size and quality, takes about four weeks with two or three breaks during the process to clean the diamond. To keep up with growing market demand, manufacturers will run at least 20 reactors at the same time with each reactor yielding about 12-20 diamonds.
Process quality and speed are critical, which is why leading lab-grown diamond manufacturers require high-performing reactors with durable components and instrumentation. Mass flow controllers (MFCs) are critical components in a reactor, managing the precise delivery of gases onto a seed crystal, via two main production methods:
- Chemical Vapor Deposition (CVD) and
- High-Pressure/High-Temperature (HPHT)
Controlling pressure is another important factor in delivering better process results. With its proven performance in critical gas flow and pressure control technology, Brooks Instrument is providing its technical expertise to support this fast-growing market, helping lab-grown diamond manufacturers reduce process time and increase yields with high-performing instrumentation.
Application Requirements
During their weeks long production campaigns, diamond manufacturers require a consistent coating thickness and uniformity along with high yields and throughput. These results are made possible with premium instrumentation that provides:
- Superior long-term zero stability for accurate, repeatable gas control to maintain critical process parameters and less frequent instrument calibration between production campaigns
- Highly accurate control of vacuum and pressure for different stages during a production campaign
Process Solution
During the chemical vapor deposition (CVD) process, four Brooks Instrument SLA5800 mass flow controllers in a gas box precisely deliver hydrocarbon gas, mostly methane, H2, N2, and O2 to the reactor where a substrate holder of carbon atom seeds is placed. Additionally, a Brooks Instrument SLA5850 back pressure controller not only controls the pressure levels but also indirectly controls the temperature in the reactor, where the chamber is heated to about 900-1200°C.
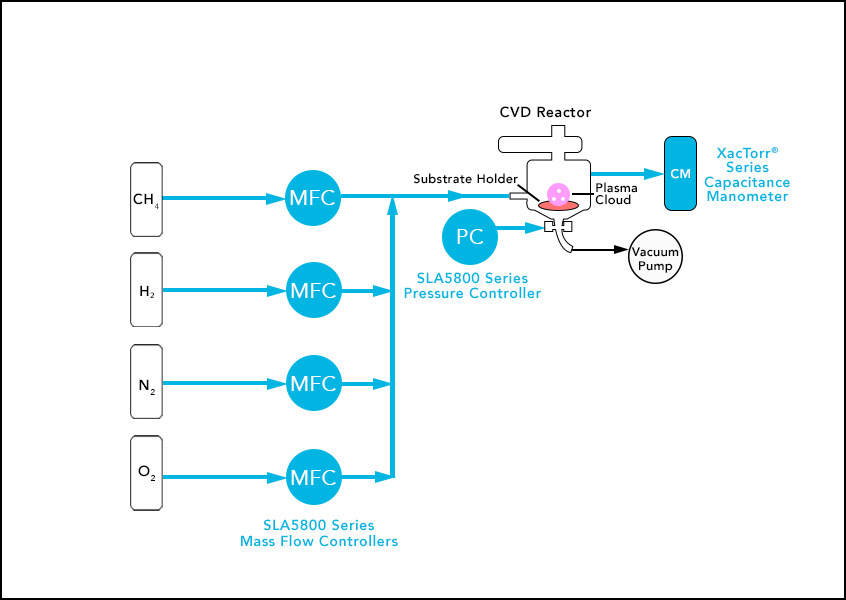
Flow scheme
A microwave beam, laser or hot filament, is the high-energy source in the reactor, forcing the carbon to precipitate out of a plasma cloud and deposit onto a seed crystal. A Brooks Instrument XacTorr® Series accurately controls vacuum levels from 20 Torr – 300 Torr. The XacTorr® Series is unique in that it is engineered with several design features that improve measurement stability and the lifetime of the instrument compared to other offerings in the market. Diamonds are removed every few hours to have the top surface polished, removing any non-diamond carbon before returning the substrate holder into the reactor for further processing.
A growing number of diamond manufacturers all over the world are specifying mass flow controllers and pressure control products from Brooks Instrument. The long-term stability, high accuracy and easy integration into various process software control systems make our gas flow and vacuum measurement and control instruments the preferred choice for high productivity tools with challenging uniformity requirements. Additionally, these manufacturers rely on local service from Brooks Instrument factory-certified flow experts when calibration may be required to support their equipment that runs continuously.